Dedicated to Serve.
Built to Execute.
There’s enough uncertainty in today’s market. When overwhelmed shippers need service and solutions they can trust, they turn to Red Classic.
Red Classic is driven to deliver. Our team of industry experts are equipped with the knowledge and resources to empower today’s most nimble brands. We provide our partners with ease and peace of mind, while helping them protect their brands, serve their customers and increase their agility. As one of the few large carriers with comprehensive fleet maintenance capabilities, Red Classic is a complete transportation partner.
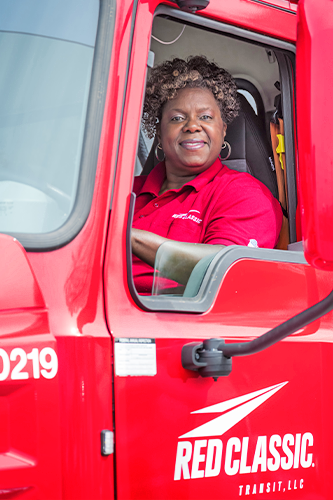
Safety
Peace of mind with safe, intact & on-time delivery
Service
Quick, friendly responses with solutions 24/7
Customization
Tailored solutions and cost efficiency
Longevity
Financial stability with history of proven results
Technology
Peace of mind and seamless communication